6 Indicators Your Work Instructions Could Benefit from a Digital Upgrade
With digital work instructions, Inservio can provide employees with access to modernized instructional materials, enabling a level of interaction and engagement that printed manuals cannot offer.
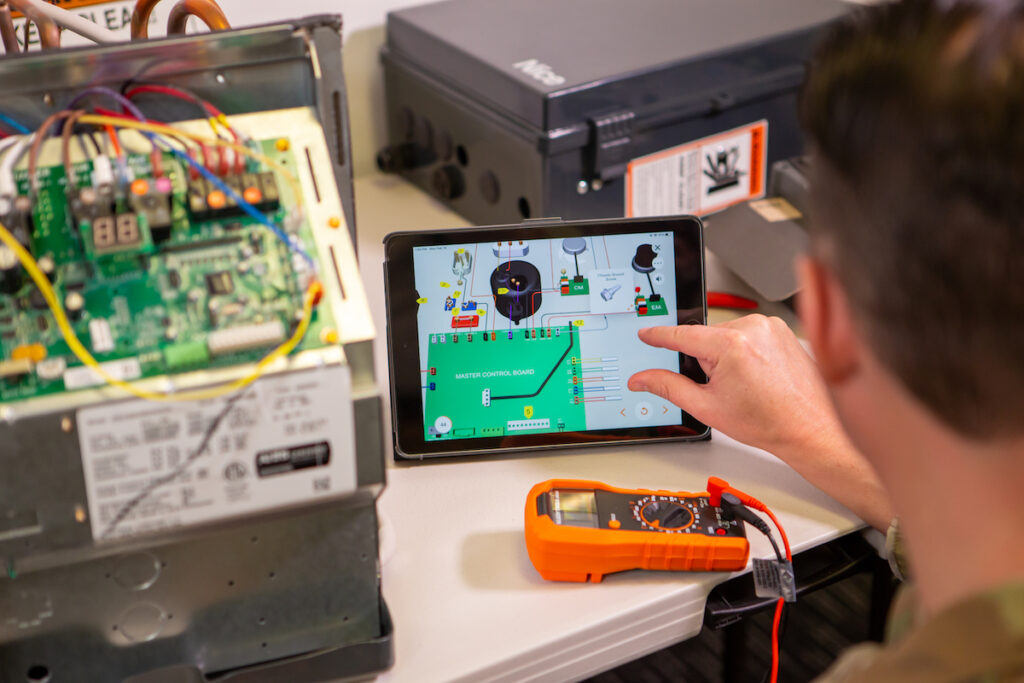
Effective work instructions are essential for building a successful team that consistently produces high-quality work. Unfortunately, many companies relying on outdated instruction and training methods place their employees and operations at a significant disadvantage, potentially leading to costly errors, wasted time and resources, and quality concerns.
Upgrading your work instructions to a digital format is an effective way to address these issues. With Inservio’s digital work instructions software, you can provide employees with access to modernized instructional materials that facilitate a level of interaction and engagement not achievable with printed instructions.
Transitioning from traditional manuals to paperless work instructions not only enhances your operations but also makes your training more effective and keeps your employees safer. Here are six key signs indicating that you’re ready for digital work instructions.
1. Outdated or Inefficient Processes
The first indication that it’s time to revise your work instruction strategy is when your current methods create more problems than they solve. For example, printed manuals can be challenging and time-consuming to update. You not only need to make corrections and additions but also develop a plan to ensure that everyone receives the revised version.
Relying solely on verbal instructions without any visual aids in the field can also lead to difficulties. Research shows that visuals can enhance learning by up to 400%, so training employees without visual reinforcement may hinder their comprehension and knowledge retention.
Ultimately, outdated and inefficient work instruction processes can negatively impact your operations, leading to excessive manufacturing errors, rework, and delays. Inservio’s digital work instructions can resolve these issues by offering mobile 3D visuals and interactive instructions, thereby enhancing employee training and improving overall efficiency.
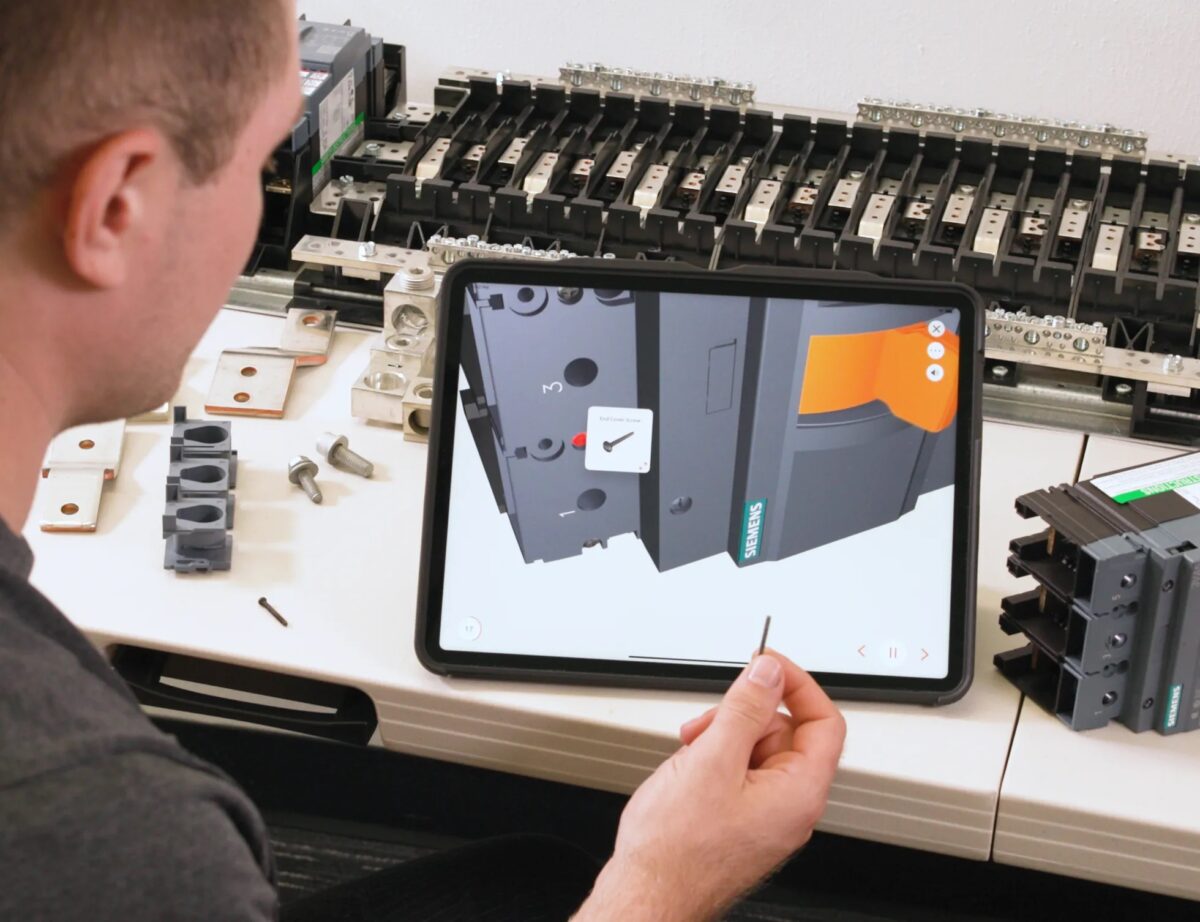
2. Lack of Standardization
To uphold a high standard of quality across your operations, it’s crucial that all employees receive uniform information regarding the steps they need to follow and how to meet your company’s standards. Inconsistent instructions can lead to confusion among your team and result in varying outcomes when executing tasks in the field.
This issue often arises when relying on printed instructions, as employees may possess different versions. For instance, a long-term employee might refer to an outdated manual instead of the latest version, while a new employee may lack awareness of past procedures or requirements. Even minor discrepancies can lead to misunderstandings and hinder collaboration among team members.
With digital work instructions, every employee has access to the same up-to-date information. This standardization guarantees product quality and ensures compliance with both internal and external standards and regulations. Additionally, it promotes trust and collaboration among employees, as they will share a common understanding of the practices within your organization.
3. Difficulty in Updating Instructions
Keeping paper instructions up to date can be logistically challenging, particularly when it comes to distribution. Along with distributing updated manuals, you also need to announce the changes and ensure that employees return or dispose of any previous versions in their possession. Frequent printing and distribution of new instructions can be costly, leading some companies to neglect regular updates. This can contribute to work errors and inefficiencies.
In contrast, digital work instruction software allows for quick and easy near real-time updates. Technicians will always have access to the most current information, eliminating the waste of time and money associated with printing and distributing manuals. Furthermore, you can make changes as often as needed, ensuring that employees receive the best possible instructions at all times.
4. Limited Accessibility
One of the most frustrating aspects of paper-based instructions is that they’re not always readily accessible when needed. For example, an employee relying on a hard-copy manual may not have it available while in the field, which is often when they need it the most.
By ensuring that instructions are easily accessible to field technicians—even those in remote locations—you enable them to complete their work more quickly and accurately. With digital 3D work instructions, these employees can use mobile devices to access the information they require, no matter where they are working.
5. Poor User Engagement in Training
If you notice that your employees frequently struggle to follow the steps outlined in their paper manuals or find it challenging to stay engaged during training sessions, a digital transformation may be the solution. Interactive work instructions are inherently more engaging, whether employees are using them during training, on the shop floor, or in the field.
Digital instructions differ from traditional paper manuals in that they accommodate various learning styles, including auditory, visual, and kinesthetic learners, through active participation and multimedia content. As a result, employees are more likely to pay attention, fully grasp the material, adhere to established processes, and ultimately boost productivity.
6. High Safety Risks and Errors
Work instruction software for manufacturing and other industries plays a vital role in protecting employees from dangerous errors that could jeopardize their health or well-being. Unclear or outdated instructions can lead to mistakes and create hazardous conditions, increasing the likelihood of safety regulation violations that could result in fines or penalties for your company.
By offering clear, up-to-date guidance, work instruction software mitigates these risks. With real-world simulations, employees can learn from their mistakes in a low-risk environment. Enhanced instructions not only help safeguard your team but also ensure your organization remains compliant with safety regulations.
Digitize Your Work Instructions with Inservio
If you’re ready to modernize your work instructions, Inservio is here to help. With user-friendly, engaging, and effective digital work instruction software, Inservio reduces your employees’ cognitive load and personalizes their experience. The ability to download instructions for offline use ensures that your employees and field technicians can access essential information on the go.
Inservio also meets the diverse needs of various industries and learning styles by providing 3D interactive instructions for mobile devices, as well as immersive 3D instructions designed for training on Apple Vision Pro.
Request a demo today to discover how interactive work instructions can enhance your employee training and improve overall business performance.